HEAVY IRON NEWS
Ultrasonic Measuring Provides Greater Well Efficiency
- By Design Team
- •
- 22 Dec, 2015
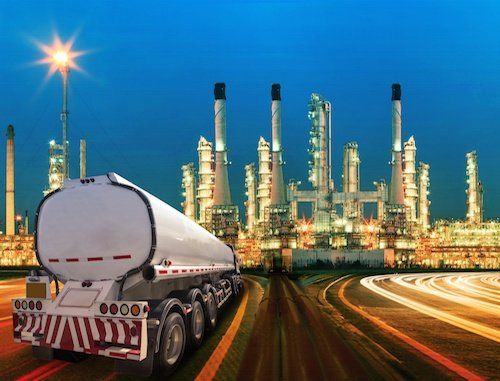
New, updated ultrasonic measuring techniques may be able to provide far better efficiency within the oil and gas industry, ultimately leading to improved profit for oil suppliers. The new sensors, developed by the UK company Permasense, are permanently installed in the field, sending back critical data to engineering personnel regarding the current status of equipment. These sensors are wireless and ultrasonic, able to easily monitor wall thickness and density.
ADVANTAGES TO THE PERMASENSE SENSOR
ULTRASONIC WAVES FOR NON-INVASIVE DETECTION
MORE EFFECTIVE THAN THE PREVIOUS ALTERNATIVES
Though manual ultrasonic inspection can be completed, it is usually a time-consuming process. Because ultrasonic inspection only offers insight into a very specific area of the equipment, there are tens of thousands of corrosion measurement points that must be individually tested. Due to the labor intensive nature of these inspections, they are generally only done every two or three years. This can entirely miss issues that arise quickly. Comparatively, Permasense sensors can take constant readings of high risk measurement points without the need for human intervention. These measurements are consolidated and sent directly to engineers so that the data can be reviewed in real time.
Permasense sensors are additionally considered to be more accurate than manual readings. Inspectors may skip data points, measure the wrong data points, or simply use equipment in a non-standard way. This can very easily occur when there are thousands of data points to be measured. Permasense sensors do not run this risk; they are able to produce consistent and reproducible measurements.
Through the use of Permasense sensors, oil sites equipment can be more effectively and efficiently monitored, drastically improving productivity and safety. Though sensors are not a complete replacement for regular inspections, they are able to quickly alert engineers to potential failures and breaches. Following the cost of adoption, Permasense sensors can reduce expenditures on oil sites, and potentially cut down on unexpected hazards
Subscribe to Email Updates
Recent Post
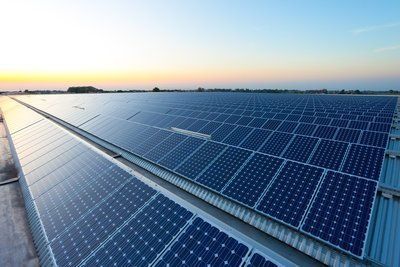
A new project in development in Oman may be able to revolutionize the way that people think about solar energy and oil and gas. The Miraah project currently being developed will use solar power in order to produce oil, thereby reducing the amount of natural gas Oman residences will need to rely upon. Ideally, the Miraah project will be able to address many of the outstanding issues with solar technology related to energy capture, while creating a more efficient and effective method of oil production. |
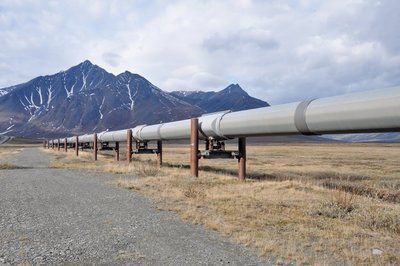
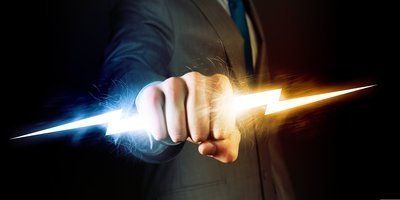
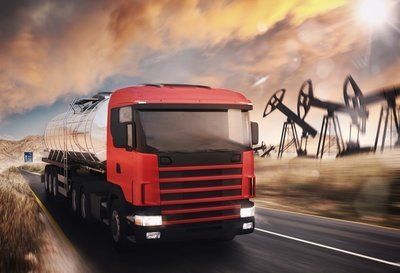
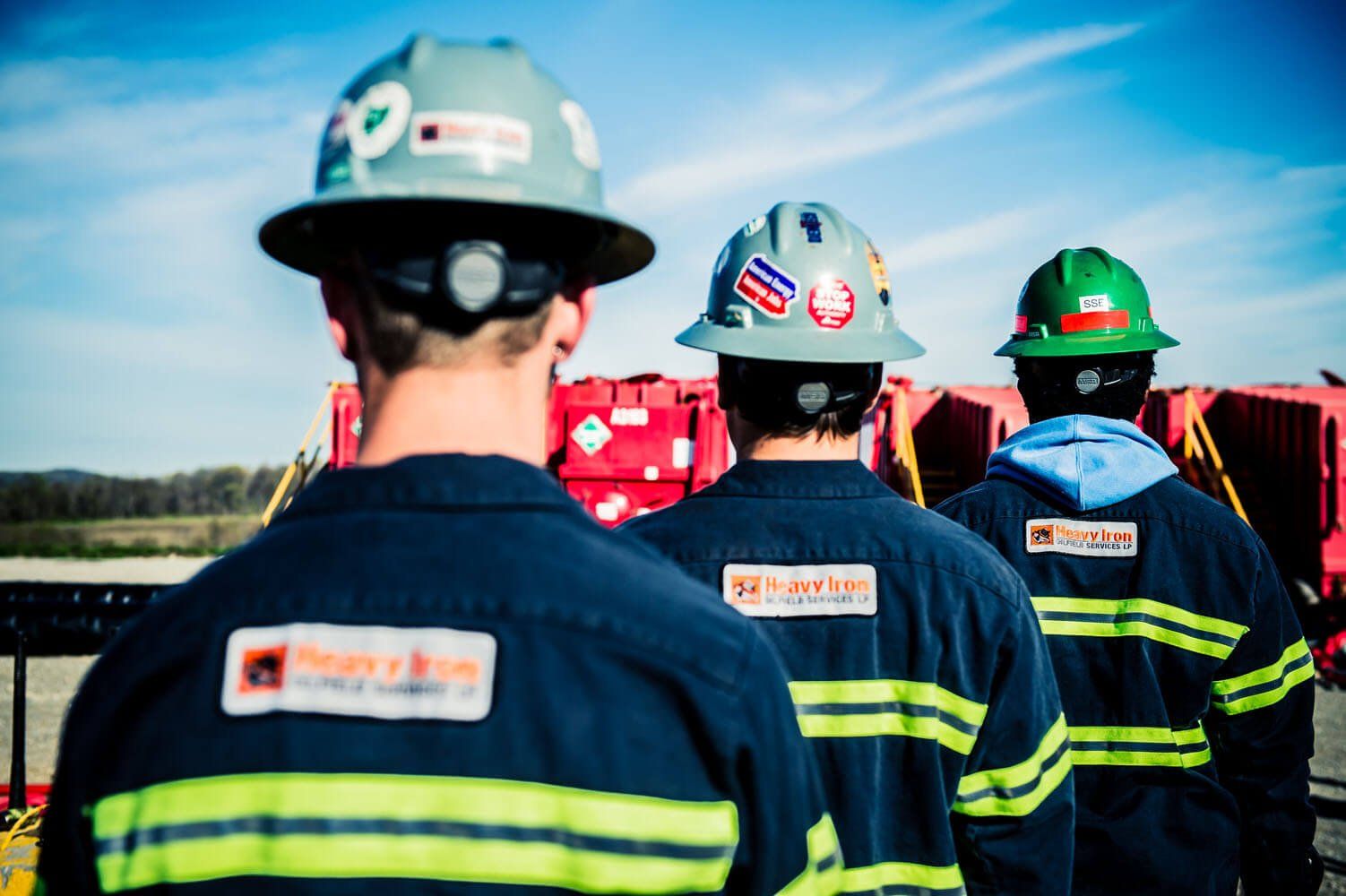